Silicon Steel vs Ferrite Cores: A Comprehensive Selection Guide for Different Applications (2025)
- LaminaCore Solutions
- Mar 19
- 9 min read
Updated: Jul 6
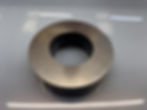
Did you know that selecting the wrong core material can reduce your transformer's efficiency by up to 30%? When it comes to electromagnetic components, the choice between silicon steel and ferrite cores isn't merely academic—it can make or break your design! As engineers, we're constantly weighing the trade-offs between these two popular materials. In this comprehensive guide, we'll break down the essential characteristics, advantages, and ideal applications for both silicon steel and ferrite cores, helping you make informed decisions for your specific requirements.
Core Material Fundamentals: Understanding Silicon Steel and Ferrite
Silicon steel, also known as electrical steel, is an iron-silicon alloy specifically engineered for electromagnetic applications. With silicon content typically ranging from 2-6.5%, these materials offer enhanced magnetic properties compared to standard steel. The addition of silicon increases the material's electrical resistivity, which helps reduce eddy current losses—a critical factor in core performance.
Ferrite cores, on the other hand, are ceramic compounds primarily composed of iron oxide combined with other metallic elements such as manganese, zinc, or nickel. These materials emerged in the mid-20th century as alternatives to metal cores, particularly for higher frequency applications where metal cores become inefficient.
The history of these materials reflects the evolving needs of electrical engineering. Silicon steel became commercially viable in the early 1900s and revolutionised power distribution, while ferrites gained prominence in the 1950s with the advent of higher frequency electronics and telecommunications.
When comparing these materials, we must consider several key magnetic parameters: permeability, saturation flux density, core losses, and temperature stability. Each of these characteristics plays a crucial role in determining which material is most suitable for a specific application.
Physical and Magnetic Properties Comparison
The most fundamental difference between silicon steel and ferrite cores lies in their magnetic properties. Silicon steel boasts an impressive saturation flux density of approximately 1.8-2.0 Tesla, significantly higher than ferrite's typical range of 0.3-0.5 Tesla. This difference has profound implications for power handling capability and core size requirements.
Permeability—a measure of how easily a magnetic field can be established in a material—also differs markedly. Silicon steel typically offers initial permeabilities in the range of 2,000-5,000, while ferrites can range from 1,000 to over 15,000 depending on composition. Higher permeability allows for more efficient energy transfer at lower field strengths.
Temperature stability presents another critical distinction. Silicon steel maintains consistent performance up to about 150°C, after which its properties degrade. Many ferrite materials, however, maintain stability at higher temperatures, with Curie temperatures (the point at which magnetic properties are lost) ranging from 120°C to over 500°C depending on composition.
Core losses—the energy wasted as heat during operation—follow different patterns in these materials. Silicon steel suffers from significant eddy current losses that increase with frequency, necessitating thin laminations to mitigate this effect. Ferrites, with their inherently high resistivity, experience minimal eddy current losses but can have higher hysteresis losses at certain operating points.
From a physical perspective, silicon steel is significantly denser (7.65 g/cm³) compared to ferrites (4.5-5.0 g/cm³), making ferrite cores considerably lighter for the same volume. However, silicon steel offers superior mechanical strength, while ferrites tend to be brittle and susceptible to cracking if subjected to mechanical stress.
Silicon Steel Cores: Advantages and Limitations
The primary advantage of silicon steel is its exceptional saturation flux density. This property enables cores to handle higher magnetic flux before saturating, allowing for smaller core sizes for a given power level. In power transmission and distribution transformers, this translates to more compact and cost-effective designs.
Silicon steel truly shines in low-frequency applications, particularly around the standard mains frequencies of 50-60 Hz. At these frequencies, properly laminated silicon steel cores offer an optimal balance of cost and performance that's difficult to match with other materials.
The manufacturing process for silicon steel has evolved to offer different grain structures, with grain-oriented (GO) and non-oriented (NO) variants available. GO silicon steel, with magnetic domains aligned in the rolling direction, offers superior performance when flux paths can be designed along this preferred direction. NO variants provide more uniform properties in different directions, making them suitable for motors and generators where flux paths are more complex.
One of the most significant challenges with silicon steel is managing eddy currents. As electromagnetic fields change, they induce currents within the conductive material that generate heat and waste energy. Manufacturers address this by creating thin laminations—sheets as thin as 0.18-0.35mm—insulated from each other to break up these current paths. Thinner laminations allow for better high-frequency performance but increase manufacturing complexity and cost.
Weight can also be a limitation in some applications. With its high density, silicon steel cores can add significant weight to devices where portability or mounting constraints are concerns. This limitation becomes particularly relevant in aerospace, automotive, and portable device applications.
Ferrite Cores: Advantages and Limitations
Ferrite cores come into their own at higher frequencies, typically above 10 kHz. Their high electrical resistivity—often millions of times greater than silicon steel—drastically reduces eddy current losses, allowing them to operate efficiently where silicon steel would become prohibitively inefficient.
This high-frequency performance makes ferrites the material of choice for switch-mode power supplies, high-frequency transformers, and modern power electronics. As electronic devices continue to operate at higher switching frequencies to reduce size and increase efficiency, ferrites have become increasingly important.
Manufacturing versatility represents another significant advantage of ferrite cores. The ceramic nature of these materials allows them to be moulded into complex shapes before sintering (heat treatment), enabling a wide variety of geometries optimised for specific applications. Common shapes include toroids, E-cores, pot cores, and planar cores, each offering distinct advantages for different circuit requirements.
However, ferrites aren't without limitations. Their lower saturation flux density means larger cores are required to handle the same power levels as silicon steel, particularly in high-power applications. This limitation becomes less significant at higher frequencies, where core losses rather than saturation typically determine size requirements.
Temperature stability in ferrites presents a complex picture. While some compositions maintain consistent properties across wide temperature ranges, others exhibit significant variation in permeability with temperature. Additionally, ferrites are susceptible to thermal shock and can crack if subjected to rapid temperature changes.
The brittle nature of ferrite materials presents manufacturing and handling challenges. Cores can chip or crack during assembly or if subjected to mechanical stress during operation. This fragility necessitates careful design considerations, particularly in high-vibration environments or applications requiring high mechanical resilience.
Application-Specific Selection Guide
Power Transformers (50-60 Hz)
For standard grid-frequency transformers, silicon steel remains the undisputed choice. Its high saturation flux density allows for compact designs capable of handling substantial power levels efficiently. Grain-oriented silicon steel laminations, typically 0.23-0.35mm thick, provide the optimal balance of performance and cost for these applications.
Switch-Mode Power Supplies
Modern switch-mode power supplies operating at frequencies from 50 kHz to several MHz almost exclusively utilise ferrite cores. The high frequency operation would cause catastrophic losses in silicon steel. Manganese-zinc (MnZn) ferrites typically serve applications up to about 1 MHz, while nickel-zinc (NiZn) ferrites extend performance into the multi-MHz range.
Inductors for Power Electronics
For power filtering inductors, the choice depends on frequency and current levels. Low-frequency, high-current applications may still benefit from silicon steel, while higher frequencies favour ferrites. Powder iron cores—composites containing small iron particles in an insulating binder—often provide a middle ground for moderate frequencies with DC bias requirements.
Current Transformers and Sensing
Current measurement applications require cores with highly stable magnetic properties and excellent linearity. Nanocrystalline materials often provide the best performance here, but high-quality silicon steel serves well in grid-frequency applications, while ferrites excel in higher-frequency measurement scenarios.
EMI Suppression Components
Electromagnetic interference suppression demands materials effective at high frequencies—typically from hundreds of kHz to hundreds of MHz. NiZn ferrites dominate this space due to their high resistivity and stable performance across broad frequency ranges. They're commonly formed into sleeves or beads that can be placed around cables to attenuate unwanted high-frequency noise.
Wireless Power Transfer
Resonant inductive coupling for wireless power operates in the kHz to MHz range, making ferrite the natural choice. These applications benefit from ferrite's low losses at higher frequencies and the ability to shape the magnetic field through custom core geometries. Silicon steel would be entirely unsuitable due to prohibitive losses at these frequencies.
Automotive Applications
The automotive sector presents unique challenges, with harsh environmental conditions and strict space and weight constraints. Ferrites serve in ignition coils, sensors, and high-frequency converters, while silicon steel finds use in alternators and low-frequency transformers. The increasing electrification of vehicles has driven development of advanced core materials optimised for automotive environments.
Cost-Benefit Analysis and Economic Considerations
The raw material cost per unit volume generally favours silicon steel, which can be 2-5 times less expensive than specialised ferrite compositions. However, this initial cost advantage must be weighed against several factors:
Manufacturing complexity: Silicon steel requires lamination, stacking, and securing, adding production costs. Ferrite manufacturing involves pressing and sintering processes that can be more economical for complex shapes.
Operational efficiency: Higher losses translate directly to wasted energy and operating costs over a device's lifetime. A more expensive core material that reduces losses by even a few percentage points can provide substantial lifetime savings in high-use applications.
Space and weight premiums: In applications where space and weight carry significant costs (aerospace, portable devices, some automotive uses), the lighter weight of ferrites may justify higher material costs.
Cooling requirements: Higher losses generate more heat, potentially necessitating additional cooling systems that add cost, weight, and complexity. Ferrite's superior high-frequency efficiency often reduces or eliminates the need for elaborate cooling in many applications.
Supply chain considerations: Silicon steel is produced by a larger number of manufacturers globally, potentially offering more stable pricing and availability than some specialised ferrite compositions.
A thorough economic analysis should consider the entire lifecycle cost rather than focusing solely on initial material expenses. For high-frequency applications operating continuously, the energy savings from ferrite cores almost always outweigh their higher initial cost compared to (unsuitable) silicon steel alternatives.
Emerging Trends and Future Developments
The magnetic materials landscape continues to evolve, with several emerging alternatives challenging the traditional silicon steel vs ferrite dichotomy:
These advanced alloys, produced by rapidly quenching molten metal to prevent crystallization, offer compelling performance benefits. With saturation flux densities approaching silicon steel but with dramatically reduced core losses, these materials bridge the gap between traditional options. Though currently more expensive, they're gaining traction in distribution transformers and high-performance applications.
Enhanced Silicon Steel
Manufacturers continue to refine silicon steel production, developing thinner laminations (down to 0.1mm) and improved grain orientation techniques. These advancements extend silicon steel's usable frequency range and reduce losses at standard frequencies.
Advanced Ferrite Compositions
Research into new ferrite formulations has yielded compositions with improved temperature stability, higher saturation flux density, and reduced losses. These specialised materials address specific application needs, from automotive environments to medical devices.
Hybrid Core Designs
Innovative approaches increasingly combine different materials within a single component to leverage the advantages of each. For example, some transformers use silicon steel for the main flux path with ferrite components in areas prone to high-frequency effects.
Industry trends toward renewable energy and electric vehicles are driving demand for more efficient electromagnetic components across all frequency ranges. This push for efficiency is accelerating research into advanced materials and optimised designs that challenge traditional selection paradigms.
Practical Selection Methodology
When selecting between silicon steel and ferrite cores, follow this systematic approach:
Define operating parameters: Determine the fundamental requirements—frequency range, power level, temperature environment, and space constraints.
Identify critical limitations: Recognise which factors cannot be compromised in your application, whether it's efficiency, size, cost, or temperature stability.
Calculate core size requirements: For both material options, calculate the required core size based on power handling needs and saturation limits.
Estimate losses: Model the expected core losses under actual operating conditions, considering both materials.
Evaluate manufacturability: Consider how the core will be incorporated into the final assembly and any special handling requirements.
Assess lifetime costs: Calculate the total cost of ownership, including initial material costs, manufacturing complexity, and operational efficiency.
Prototype and validate: When possible, test prototypes of critical designs with different core materials to verify analytical predictions.
Common pitfalls in this process include focusing too narrowly on a single parameter (such as initial cost or size), failing to consider the full operating temperature range, or not accounting for harmonics and non-sinusoidal waveforms that may significantly impact actual performance.
Industry case studies consistently show that proper core selection can improve overall device efficiency by 5-20% while potentially reducing size and weight. These benefits compound in systems using multiple magnetic components, such as power distribution systems or complex electronic devices.
Conclusion
Selecting between silicon steel and ferrite cores involves balancing numerous factors including operating frequency, power requirements, cost constraints, and space limitations. While silicon steel excels in high-power, low-frequency applications due to its superior saturation flux density, ferrite cores dominate in high-frequency scenarios where core losses become critical.
As technology continues to evolve, staying informed about the latest developments in core materials will help you optimise your designs for maximum performance and efficiency. Remember that the best choice always depends on your specific application requirements—there's no one-size-fits-all solution in the world of magnetic core materials!
For critical applications, consider consulting with material specialists or component manufacturers who can provide detailed performance data and application-specific recommendations. The right core material choice can be the difference between a mediocre design and an exceptional one, affecting everything from efficiency and thermal management to reliability and lifetime costs.
Have you faced challenges selecting between these core materials for your projects? What factors ultimately guided your decision? We'd love to hear about your experiences in the comments below!